Neben zahlreichen kleineren Rationalisierungsvorhaben durch Konstruktion, Bau und Einsatz von Sondermaschinen, insbesondere in der Handwerkzeugfertigung wurden seit 1970 eine Reihe von sogenannten Großvorhaben mit hohem Investitionsaufwand im Stammbetrieb und den anderen Kombinatsbetrieben realisiert. Im Folgenden sollen einige dieser Vorhaben im Stammbetrieb kurz vorgestellt werden. Von 1970 bis 1975 wurde im Stammbetrieb ursprünglich zur Produktion von Werkstücklage- und -sicherungseinrichtungen ein Großvorhaben mit einem Investaufwand von mehr als 260 Mio. Mark, davon über 80 Mio. Mark für den Bau realisiert. Im Zuge dieses Vorhabens wurden u. a. ein Kompaktbau für die Produktion, eine Betriebsgaststätte, ein Objekt für die praktische Berufsausbildung, ein Ölheizwerk, ein Sozialgebäude für die Schmiede, eine Kinderkombination[1] und eine Arzt-/Zahnarztstation errichtet. Infolge eines Strukturwandels in der Volkswirtschaft wurden in den neuen Hallen dann spanende Blankwerkzeuge und Handwerkzeuge produziert.
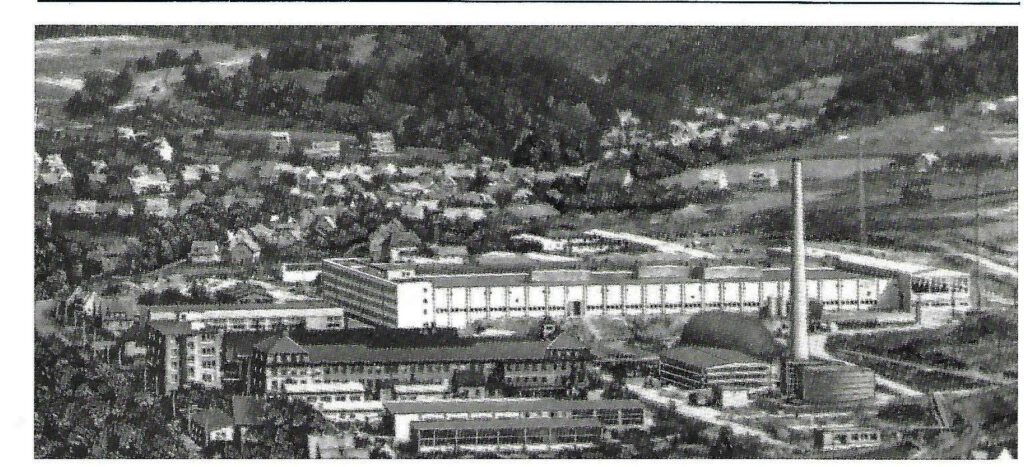
Zur besseren Versorgung der DDR-Volkswirtschaft mit Basishaltern (Werkzeugaufnahmen) wurde von 1978 bis 1981 ein „integrierter gegenstandsorientierter Fertigungsabschnitt“ (IGFA) aufgebaut. Dafür wurden Investitionen in Höhe von 110 Mio. Mark aufgewendet. Der IGFA Basishalter umfasste neben einem Hochregallager eine rechnergestützte Prozesssteuerung und moderne NC-Maschinen (Bild 21). Leider musste der IGFA Basishalter nach wenigen Jahren in Zusammenhang mit den Anforderungen aus anderen Automatisierungsvorhaben der DDR-Wirtschaft wieder aufgegeben werden.
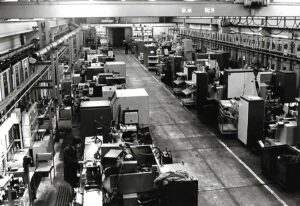
IGFA Basishalter
Auf der Basis einer Aufgabenstellung der 11. ZK-Tagung der SED und des Beschlusses des ZK-Sekretariats vom 6.7.1980 wurde in allen Kombinaten und Betrieben eine Umstellung der Heizwerke von Erdöl auf Braunkohle durchgeführt. Eine der Hauptursachen für diese Maßnahme war neben der internationalen Ölkrise auch die Reduzierung der Erdöllieferungen aus der Sowjetunion entgegen den langfristigen Vereinbarungen.
Betroffen von dieser Energieträgerumstellung (ETU) war u. a. auch der Stammbetrieb, vorwiegend mit den Werken 1 und 2. In den Jahren 1982 bis 1985 wurden neben einem Investaufwand von über 30 Mio. Mark vor allem umfangreiche personelle und materielle Ressourcen in Vorbereitung und Durchführung der ETU gebunden. Die teilweise stockende und witterungsabhängige Versorgung mit Braunkohle führte zu erheblichen Problemen in der Produktionsdurchführung. Führende Wirtschaftswissenschaftler und -historiker sahen in dieser Maßnahme eine der entscheidenden Ursachen für den Niedergang der DDR-Wirtschaft Ende der 80er Jahre.
1983/1984 erfolgte eine enorme Kapazitätserweiterung der Mähklingenfertigung über ein Automatisierungsvorhaben (ATV) mit über 40 Mio. Mark Investitionen und einem sehr hohen Automatisierungsgrad (Bild 23). Bei einer Stundenleistung von 10.000 Stück betrug die Jahresproduktion etwa 35 Mio. Stück dreieckverzahnte Mähmesserklingen (7 Typen) für die Ausrüstung der Erntemaschinen des VEB Kombinat Fortschritt Landmaschinen Neustadt und für den Export ins sozialistische Wirtschaftsgebiet. Der gesamte Fertigungsabschnitt von ca. 70 m Länge in starrer Verkettung umfasste im Wesentlichen folgende Bearbeitungsschritte
- Weichbearbeitung durch Stanzen, Prägen und Senken der Aufnahmebohrungen,
- Wärmebehandlung durch Zwischenstufenvergüten, Reinigen und nachfolgendes Ordnen der Klingen,
- Hartbearbeitung durch Schleifen der Verzahnung und
- Konservieren und Verpacken der Klingen mittels IR-Technik.
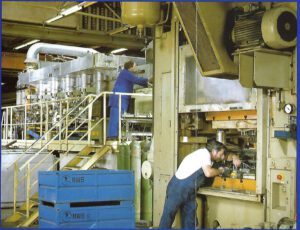
Hauptauftragnehmer war das Kombinat Umformtechnik (für „technologische Ausrüstungen“) einschließlich weiterer Unterauftragnehmer und den kombinatseigenen Ratiomittelbau-Kapazitäten in Schmalkalden und Schmölln. Dank des hohen Einsatzes aller Beteiligten konnte das ATV Mähklingen in weniger als einem Jahr realisiert werden.
Voraussetzung für die Automatisierung war eine vorangegangene Materialumstellung auf 50CrV4 im Rahmen einer Erzeugnisentwicklung. 1996 kam eine vollautomatische Transportsteuerung mit automatischer Stückzahlerfassung und Ermittlung der Maschinenlaufzeiten hinzu. Die Einführung der „rollenden Woche“, d. h. eines durchgehenden Dreischichtbetriebes einschließlich der Wochenenden im ATV Mähklingen stieß bei den Arbeitern zunächst auf wenig Gegenliebe, wurde jedoch durch eine überdurchschnittliche Entlohnung ausgeglichen. Entsprechend unbeliebt war daher die Rückkehr zum normalen Schichtbetrieb infolge des wegfallenden Exports in die Sowjetunion aufgrund der Aufnahme einer dortigen Eigenproduktion.
Das ATV Mähklinge bildete die Grundlage für die Privatisierung des Komplexes Technische Messer im Werk 1 des Stammbetriebes und die ebenso erfolgreiche Entwicklung der neu entstandenen MWS Schneidwerkzeuge GmbH Schmalkalden.
Auf Grundlage mehrerer Politbürobeschlüsse der SED wurden seitens des WKS im Auftrag des Ministeriums ein Automatisierungsvorhaben zur Erreichung der vollen Bedarfsdeckung bei ausgewählten Handwerkzeugsortimenten unter dem Arbeitstitel „Automatisierung der Schmiede-, mechanischen Fertigungs- und Oberflächenbehandlungsprozessen für Zangensortimente“ konzipiert, das aber in der vorgeschlagenen Form vom Ministerium nicht bestätigt wurde.
In einer Beratung im MWV am 28.08.1984 wurde empfohlen, ein ATV in Verantwortung des Stammbetriebes zur Sicherung der Rohlingsbereitstellung zu konzipieren und ein „Kompensationsvorhaben Handwerkzeuge“ gemeinsam mit dem Außenhandelsbetrieb (AHB) WMW-Export-Import. Im Rahmen des Kompensationsvorhabens wurden über den AHB Komplettangebote von Rohlingsherstellung bis zur Kennzeichnung und Verpackung über die Firmen Warimex (WAN), Westberlin, und Ferrostaal, Essen sowie Einzelangebote zu den Komplexen Schmieden von Zangenrohlingen, Kaltumformung von Steckschlüsselrohlingen, Schleifen und Polieren von Handwerkzeugen sowie Reinigen, Konservieren und Verpacken über die Fa. Wittenbecher, Westberlin eingeholt. Einbezogen in die Angebotstätigkeit waren die westdeutschen Firmen Lasco, Eumuco, National Machinery, Graebener, Schuler, Komatsu, C. K. Walther, Rösler, Hau, Hahn&Kolb, Metabo, Niederberger, Montanwerke Walter, Illig, ACME, KMU G. Krüger, IWK Verpackungstechnik, Siebler, Kallfass, W u D und Vempack.
Ziel beider zusammenhängender Vorhaben mit einem geplanten Investaufwand von 176 Mio. Mark bzw. 188 Mio. Mark war die Erreichung der vollen Bedarfsdeckung im Zangensortiment im Jahre 1980. Leider konnten beide Vorhaben aufgrund fehlender finanzieller und materieller Einordnungsbedingungen nicht realisiert werden. Nach der Wende stellte es sich heraus, dass die beiden „Westberliner“ Firmen WAN und Wittenbecher waschechte DDR-Firmen aus dem Koko-Imperium des Alexander Schalck-Golodkowski waren.
In den Jahren ab 1986 spielte das WKS eine entscheidende Rolle bei der Versorgung der zahlreichen Automatisierungsvorhaben in der Volkswirtschaft der DDR mit leistungsfähigen Standard- und Sonderwerkzeugen sowie Werkzeugaufnahmen.
Zur Verbesserung der Bedarfsdeckung bei Werkzeugaufnahmen (Basishaltern), WSP-Fräswerkzeugen, Ausbohrwerkzeugen und gelöteten HM-Werkzeugen einschließlich der Produktionseinführung des Variablen Werkzeugsystems (VWS) wurde für den Zeitraum 07/89 bis 12/90 ein ATV I „Werkzeugsysteme für den automatischen Wechsel“ im Stammbetrieb geplant und teilweise realisiert. Der geplante Investaufwand betrug 80,5 Mio. Mark, davon 15 Mio. Valutamark-Importe aus dem nichtsozialistischen Wirtschaftsgebiet (NSW). In die Vorbereitung und Teilrealisierung war auch die Industriekooperation WKS-Stammbetrieb – Montanwerke Walter, Tübingen, (siehe …) einbezogen.
Ein weiteres ATV II „Automatisierung Basishalter“ zur bedarfsdeckenden Produktion von modularen Werkzeugsystemen, Werkzeugaufnahmen und Hochleistungswerkzeugen war von 1991 – 1995 geplant mit einem Investaufwand von 346 Mio. Mark davon 35 Mio. Valutamark NSW-Importe.
Die im Rahmen der Automatisierungsvorhaben im Stammbetrieb geschaffenen technologischen Lösungen durch den Einsatz moderner CNC- und Rechentechnik bildeten eine der Grundlagen für die erfolgreiche Privatisierung dieser Produktionsabschnitte nach 1990.