Die staatlichen Planauflagen sahen für das WKS jährliche Steigerungsraten hinsichtlich der Erhöhung der industriellen Warenproduktion (IWP) und/oder Kosteneinsparungen (u. a. Material- und Arbeitsaufwand) vor. Diese waren neben der Entwicklung neuer Erzeugnisse im Wesentlichen über die Ergebnisse der technologischen Forschung zu realisieren. Außerdem bedingten neue und weiterentwickelte Erzeugnisse neue Herstellungsverfahren und umgekehrt. Jede technologische Neuerung führte auch zu einem neuen bzw. weiterentwickelten Erzeugnis.
Im Folgenden soll auf einige Verfahrensentwicklungen im Stammbetrieb, meist in enger Zusammenarbeit mit dem Forschungszentrum, eingegangen werden.
Im Rahmen einer ab 1979 in der DDR eingeleiteten Automatisierungskampagne durch den Einsatz von Industrierobotern und Handhabetechnik wurde im Stammbetrieb des WKS ein F&E-Thema „Untersuchung der Anwendungsmöglichkeiten von Manipulatoren und Industrierobotern in den Schmieden des VEB WKS-Stammbetrieb“ in Kooperation mit dem Bereich Wissenschaft Gera des zentralen Rationalisierungsbetriebes RWS Schmölln bearbeitet. Die Verteidigung der Leistungsstufe A 2 fand am 20.12.1979 statt und kam zu dem bestätigten Ergebnis, dass ein Industrierobotereinsatz beim Schmieden nicht effektiv ist, sondern – wenn überhaupt – beim Drehen rotationssymmetrischer Teile.
Ungeachtet dieses Ergebnisses stellten die Partei- und Kombinatsleitung die Aufgabe, „in Vorbereitung des X. Parteitages der SED“ den Einsatz eines Industrieroboters zur Warmumformung von Bergbauwerkzeugen als Modellfall zu realisieren. Im Schmiedekomplex verknüpfte ein Roboter IR-5-10 eine Spindelpresse mit einem Glühofen beim Warmstauchen von Schrämpicken für den Bergbau. Die Funktionserprobung des Komplexes erfolgte 9 Monate vorfristig und die Produktionswirksamkeit wurde 6 Monate vorfristig „zu Ehren des 32. Jahrestages der DDR“ erreicht – so der damalige Sprachgebrauch. Das Vorbereitungs- und Realisierungskollektiv wurde am 1. Mai 1982 mit dem Orden „Banner der Arbeit Stufe III“ ausgezeichnet.
Ende 1980 wurde auf einer ZK-Tagung und im April 1981 auf dem X. Parteitag der SED der verstärkte Einsatz der Robotertechnik in der Volkswirtschaft der DDR beschlossen. Das Gesetz über den Fünfjahrplan 1981 – 1985 enthielt als Zielstellung die Produktion und den Einsatz von 45.000 Industrierobotern, allerdings verbunden mit einer neuen Definition eines „Industrieroboters“. So wurden zu den Industrierobotern z. B. auch automatisierte Vorrichtungen und Werkstückhandhabungseinrichtungen gezählt.
Vom Ministerium für Wissenschaft und Technik wurde das WKS beauftragt, einen Einsatzfall für den Robotereinsatz zum Schmieden von Schlosserhämmern und Montagezangen zu realisieren. Dazu wurden dem WKS über eine österreichische Firma (unter Umgehung der Embargoliste der NATO!) zwei Industrieroboter E 402 der westdeutschen Firma Vereinigte Flugzeugtechnische Werke Bremen (VFW) zur Verfügung gestellt.
Nach umfangreichen Vorbereitungsmaßnahmen und Abstimmungen wurden die beiden Industrieroboter am 15.11.1982 an das WKS geliefert und ein Schmiedekomplex zum Schmieden von Schlosserhämmern realisiert. Dabei mussten zahlreiche Einrichtungen wie Transfereinrichtungen, Abgratwerkzeuge, Gesenkhalter, Temperaturmeßeinrichtungen u. a. neu entwickelt und gebaut werden sowie umfangreiche bauliche Maßnahmen (Fundamente etc.) ausgeführt werden.
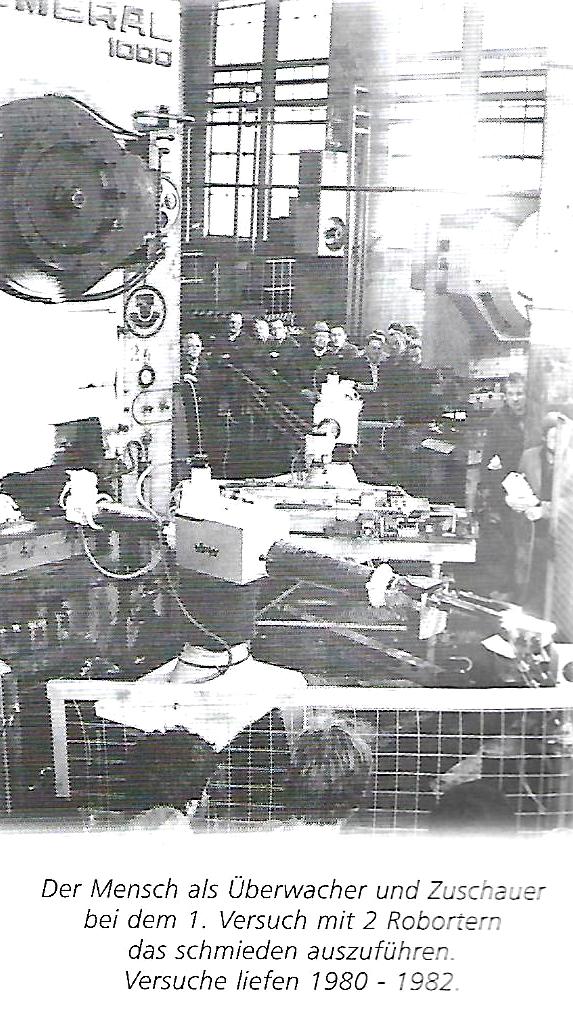
Da der automatisierte Schmiedekomplex wegen zu geringer Verfügbarkeit der gesamten Anlage aus 11 einzelnen Aggregaten trotz positiver Erprobung zu einer Reduzierung der Industriellen Warenproduktion (IWP) führte, musste das Projekt auf Betreiben der Partei- und Gewerkschaftsleitung des Werkes 2 abgebrochen werden.
Obwohl dieses Projekt zu seiner Zeit einmalig in Europa war, musste es aber der damaligen IWP-Ideologie geopfert werden. Der Generaldirektor entschied am 23.09.1983 den Abbruch des großtechnischen Versuches mit der Maßgabe, den Schmiedekomplex außerhalb der Produktion unter Einbeziehung einer Querwalze neu aufzubauen und zu erproben. Auch dieses Projekt konnte aus verschiedenen Gründen nicht realisiert werden. So waren u. a. keine Bilanzanteile für eine Querwalze verfügbar.
1975 erhielten das Ministerium für Werkzeug- und Verarbeitungsmaschinenbau (MWV) und das Ministerium für Metallurgie, Erzbergbau und Kali (MEMK) die Aufgabe, pulvergeschmiedete Handwerkzeuge zu entwickeln und zu produzieren, obwohl international zu dieser Zeit nur ausgewählte Fahrzeugteile wie Synchronringe und keine Massenartikel wie Zangen pulvermetallurgisch hergestellt wurden.
Dazu wurden zwei Staatsplanthemen im WKS-Stammbetrieb und im Eisenhüttenwerk Thale (EHW) mit der Zielstellung V11 Ende 1980 eingeordnet. Begonnen wurde mit Kombinationszangen; nach 1980 war die Erweiterung auf weitere Zangensortimente vorgesehen. EHW war für die Herstellung des Pulvers und der Rohlinge und WKS für die Fertigbearbeitung zuständig. Dazu gab es im WKS das Staatsplanthema „Entwicklung einer Technologie zur Fertigbearbeitung von pm-Kombizangen“ mit einem Unterthema bei RWS Schmölln „Konstruktion und Bau von Sondermaschinen für die Fertigbearbeitung von pm-Kombizangen“. Der Gebrauchswerttest der pm-Fertigungsmuster verlief positiv. Auch äußerlich war die pm-Kombizange nicht von einer herkömmlichen Zange zu unterscheiden (Bild 13).
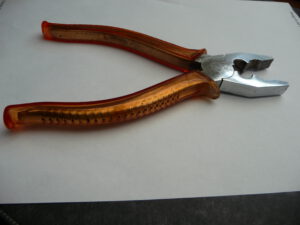
Infolge des hohen Pulverpreises bei EHW Thale kam es zu keiner Produktionseinführung, obwohl es bei der Fertigbearbeitung durch Wegfall von Arbeitsgängen zu erheblichen Kosteneinsparungen kam. Auch unter sozialistischen Bedingungen konnten sich die beteiligten Partner aber nicht auf eine Verteilung der Kosten und Erlöse einigen.
Am 15.09.1982 konnte ein Neuererkollektiv, bestehend aus Arbeitern des Produktionsbereiches Kellenfertigung im Werk IV (ehemals Fa. Kampmann) und Ingenieuren der FA Technologische Verfahrensentwicklung eine neue Technologie des Schweißens der Angel an Maurerkellen mit der Nullserienproduktion von geschweißten Maurerkellen der Größe 228 einführen.
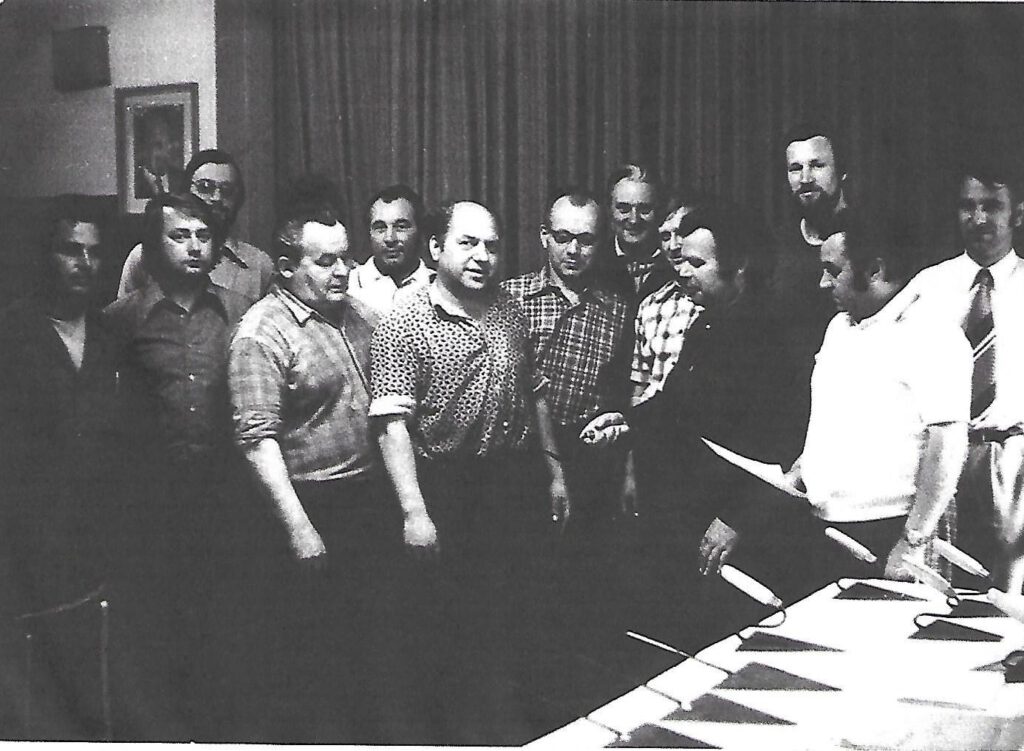
Die neue Technologie sah anstelle des bisherigen Ausreckens der Angel an Maurerkellen das Anschweißen der separat gefertigten Angel vor. Diese Technologie wurde aufgrund des verwendeten Werkstoffes selbst von den Experten des Zentralinstitutes für Schweißtechnik in Halle für nicht machbar gehalten. Auch eine Abordnung Berliner Bauarbeiter konnte erst bei einem Betriebsbesuch in Schmalkalden von dieser neuen Technologie überzeugt werden.
Aufbauend auf Voruntersuchungen des Forschungszentrums des Werkzeugmaschinenbaus Karl-Marx-Stadt wurde ab 1974 die Möglichkeit der Antihaftbeschichtung mittels PTFR-Materialien an einem breiten Sortiment von Holzbearbeitungs- und Malerwerkzeugen untersucht.
Aufgrund des notwendigen Imports des Beschichtungsmaterials aus Großbritannien beschränkte sich die Anwendung auf die neuentwickelte Bauhandsäge und Kreissägeblätter für den Heimwerker. Die Beschichtung selbst wurde in Kooperation mit einem Dresdner Chemiebetrieb durchgeführt.
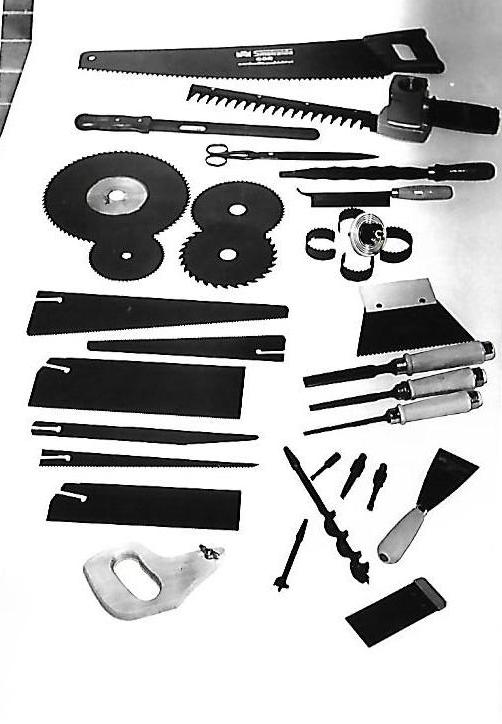
1979 wurde gemeinsam mit Technologen des Werkes 2 des Stammbetriebes das Direkttauchen von PVC-Griffen für Zangen entwickelt und erfolgreich eingeführt. Dabei gab es große Schwierigkeiten in der Bereitstellung der tauchfähigen PVC-Paste durch die Chemieindustrie der DDR aufgrund der relativ geringen benötigten Mengen. Später kam noch die Herstellung von Zangengriffen aus geschäumten PVC-Materialien hinzu.
Umfangreiche Untersuchungen zum Entgraten z. B. von Bergbauwerkzeugen mittels des TEM-Verfahrens (Thermisches Entgraten), wobei die im Zerspanungsprozess erzeugte Grate mittels einer kontrollierten Knallgasreaktion quasi verbrannt wurden, führten trotz guter Ergebnisse nicht zum Erfolg, da die Anlage nur in der BRD hergestellt wurde und wegen Valutamangel nicht importiert werden konnte.
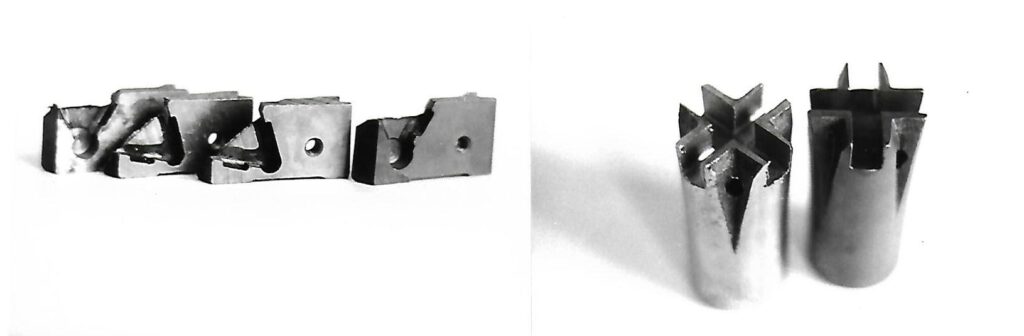
Die Substitution des Verchromens bei Ringschlüsseln und Montagezangen durch das Glanzverzinken brachte eine erhebliche Materialeinsparung bei gleichbleibenden bzw. sogar höheren Korrosionsschutzeigenschaften.
Durch die Fachabteilungen des FZWI in Karl-Marx-Stadt wurden seit den 70er Jahren zwecks Einsparung des Legierungselementes Kobalt neue kobaltarme bzw. kobaltfreie Schnellarbeitsstähle mit teilweise erhöhten Gebrauchseigenschaften entwickelt und mit Stahlwerken der DDR und Kombinatsbetrieben in die Produktion überführt. Gleichzeitig wurden die entsprechenden Wärmebehandlungstechnologien entwickelt. Zur Leistungssteigerung insbesondere bei Schnellarbeitsstahl-Werkzeugen, aber auch bei HM-Wendeschneidplatten , wurden ab Ende der 70er Jahre nach der Entwicklung und Einführung solcher Verfahren wie Dampfanlassen und Nitrieren auch neue Verfahren der Oberflächenbeschichtung mit Hartstoffen wie Titannitrid (TiN) entwickelt und in die Produktion u. a. bei Bohrwerkzeugen überführt.
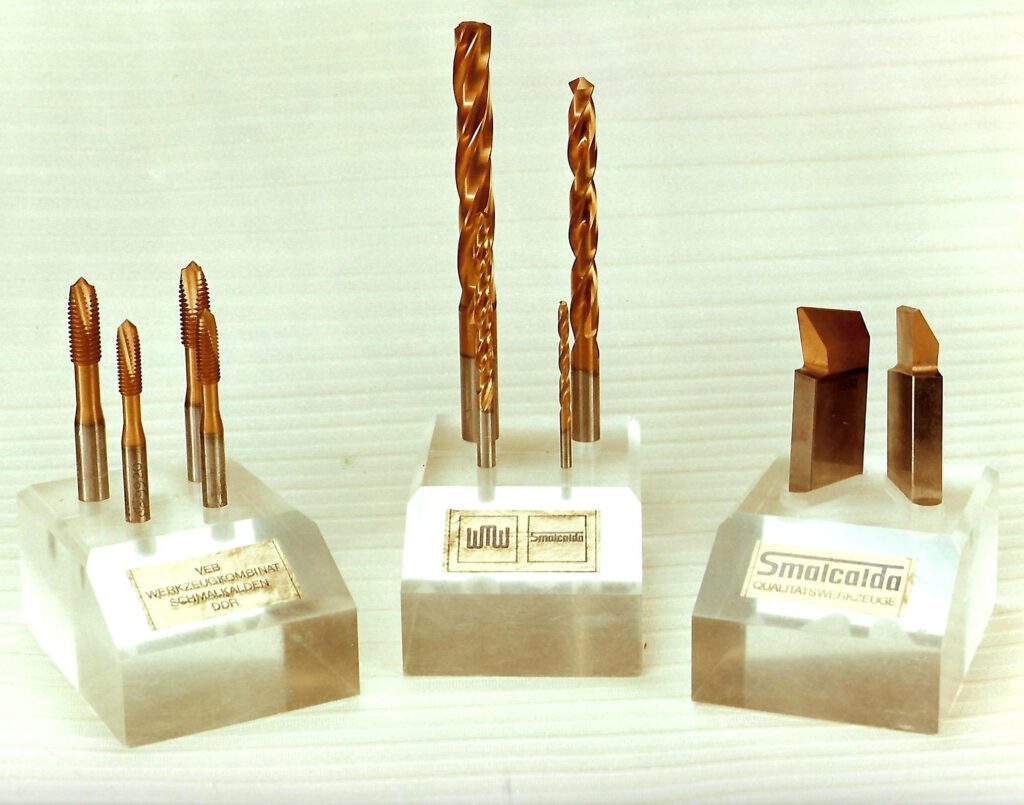
Die Werkzeugbeschichtung erfolgte im WKS nach zwei Verfahren im Vakuum,
- der reaktiven Bedampfung mit Hohlkatodenbogenverdampfer bzw.
- der reaktiven Katodenzerstäubung mit Plasmatronquelle.
Infolge der niedrigen Beschichtungstemperatur von 300 – 500 Grad Celsius konnte das Beschichten an fertigen Werkzeugen durchgeführt werden, ohne dass die Grundwerkstoffeigenschaften und die Geometrie des Werkzeuges negativ beeinflusst wurden. Im Ergebnis wurden Standzeiterhöhungen von 100 – 400 % nachgewiesen.
Neben den beiden Beschichtungsverfahren wurden in enger Kooperation mit der TH Karl-Marx-Stadt weitere weltstandsbestimmende Beschichtungsverfahren für Werkzeuge und Bauteile entwickelt und teilweise patentiert. Gleichzeitig wurden die notwendigen Anlagen konstruiert und gebaut. Zu diesen Prozessen gehörten u. a.
- der ICL – Prozess (Ion Carbon-Layer) für extrem harte Kohlenstoffschichten und
- der MECAN – Prozess (Metal-Carbide-Nitride) für Metallcarbid- und Mehrfachschichte.
Für beide Verfahren gab es internationale Lizenzwünsche z. B. aus Japan, der BRD, Österreich und Rumänien.
Gegen Ende der 80er Jahre wurden umfangreiche Untersuchungen gemeinsam mit dem Institut von Prof. Ardenne Dresden zur TiN-Beschichtung mittels der Elektronenstrahltechnologie angestellt, die jedoch nicht mehr zur Produktionswirksamkeit kamen.
Neben den erwähnten Ergebnissen der technologischen Verfahrensentwicklung wurden in enger Zusammenarbeit zwischen Erzeugnisentwicklern, Verfahrensforschern und Technologen zahlreiche Rationalisierungslösungen in der Fertigung von Handwerkzeugen und Maschinenwerkzeugen entwickelt, gebaut und in die Produktion überführt.
Leider konnten aufgrund der fehlenden Randbedingungen in der Planwirtschaft der DDR viele technologische Neuerungen, die weltstandsbestimmend waren, nicht zur Produktionsreife geführt werden, z. B. das Schleppschleifen bei Zangen oder das erwähnte Pulverschmieden von Zangen.